Centre d'excellence mécanicien, HyMEET est doté d’un parc de moyens d’essais, de mesure et d’analyse unique en Europe au service des industriels, représentant un investissement de près de 25M€.
Actuellement répartis sur les différents sites du Cetim en France, l'ensemble des équipements de laboratoire et moyens expérimentaux mettant en œuvre l’hydrogène seront dès 2025 réunis au sein d'un bâtiment d’une surface de 1 850m². L’aménagement intérieur est conçu pour accueillir les moyens expérimentaux dans des salles dédiées par typologie d’essais et par zonage ATEX mettant en œuvre de l’hydrogène sous haute pression (jusqu’à 1000 bar) et dans une gamme de température allant de la cryogénie profonde (20K) jusqu’aux températures élevées de l’hydrogène (800°C).
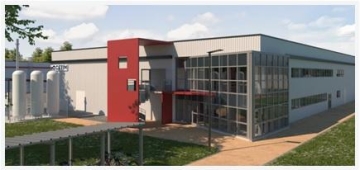
Avec HyMEET, les industriels bénéficient d'un parc unique d'équipements de pointe, associé aux 60 ans d'expertise pluridisciplinaire du Cetim en matériaux-produits-process.
Sélectionner les matériaux, comprendre et caractériser leur comportement mécanique et leur durabilité en environnement H2.
Aussi bien pour les réseaux de distribution, les équipements de production, le stockage et pour les différents usages de l’hydrogène, la tenue dans le temps et l’intégrité mécanique des matériaux en contact avec l’hydrogène est primordiale.
Les investissements du projet HyMEET, intègrent des équipements de pointe dédiés à la caractérisation du comportement des matériaux au contact de l’Hydrogène et à l’élaboration de procédures d’essais spécifiques afin de développer des méthodologies de choix raisonnés de matériaux prenant en compte la fragilisation par Hydrogène:
- Plusieurs machines de fatigue de grande capacité (15L de 80 à 400 bar) et sur une gamme de température de 70 K à 400 K pour couvrir les conditions de service en pression et en température de la chaine de valeur H2 ;
- Un dispositif expérimental de type « éprouvette creuse » pour les pressions et températures extrêmes (de type 1000 bar jusqu’à 800°C) ;
- Des bancs spécifiques pour la réalisation d’essais de fatigue sur des sous-systèmes mécaniques.
Reproduire ou simuler les conditions de vieillissement sévères
Des équipements pour accélérer les phénomènes de diffusion, étudier les phénomènes de vieillissement en environnement H2 sur tous les types de matériaux:
- Un parc de plusieurs autoclaves en H2 jusqu’à 350°C et 1000 bars pour conditionner sous pression d’hydrogène les éprouvettes métalliques avant essais mécaniques ou bien pour réaliser des essais de vieillissement de matériaux organiques longue durée (élastomère, plastiques et composites).
Caractériser la diffusion de l’hydrogène et la perméabilité des matériaux
L’analyse de la perméabilité des matériaux est primordiale pour la compréhension des phénomènes de fragilisation par hydrogène mais aussi pour la caractérisation de la perméabilité des systèmes d’étanchéité pour des applications tuyauteries, réservoirs métalliques et composites et composants sous pression.
A cette fin sont déployés :
- Des équipements de perméation électrochimique et de perméation gazeuse sur membranes métalliques sous haute pression (400 bar) pour évaluer des revêtements barrières dédiés la protection des éléments en contact de l’hydrogène ;
- Des bancs spécifiques intégrant des cellules de perméation haute pression sous H2 et température élevée et basse pour l’étude de la perméabilité des matériaux organiques polymères ou composite.
Caractériser les matériaux
La connaissance précise de la teneur et de la nature en H2 dans les matériaux métalliques, après phase de chargement, avant et après caractérisation mécanique est extrêmement importante pour appréhender la compréhension des mécanismes de fragilisation par hydrogène.
A cette fin, sont déployés :
- Un équipement de Spectrométrie de Désorption Thermique (TDS) ;
- Plusieurs chromatographes et spectromètres de masse pour permettre l’analyse de gaz ;
- Des équipements de caractérisation de surface métallurgiques ;
- Des équipements de caractérisation des propriétés thermiques des matériaux.
Reproduire les conditions de fonctionnement cryogéniques
Les application hydrogène liquide et le domaine de la cryogénie profonde à l’échelle industrielle qui lui sont associées posent de nouveaux verrous technologiques concernant la conception et la durabilité des équipements qui seront nécessaires à son déploiement.
- Un liquéfacteur d’hélium et d’hydrogène pour la réalisation d’essais de caractérisation de composants, capteurs, matériaux en conditions très basses températures ;
- Une machine de Thermo Mechanical Analysis (TMA) pour la mesure des coefficients de dilatation de matériaux jusqu’à des températures de 4K ;
- Une machine de fatigue/traction en environnement cryogénique sec (20 K) mettant en œuvre un cryocooler He complètera le parc machines pour les essais cryogéniques dès 2025.
Développer, évaluer et sélectionner les solutions d’étanchéité et leur durabilité
La maîtrise du confinement des installations et équipements industriels, et donc des étanchéités associées, est un sujet de premier ordre pour la maîtrise de la sécurité en environnement hydrogène.
Dans ce cadre différents moyens expérimentaux permettant de caractériser les performances et la durabilité des systèmes d’étanchéité sont déployés :
- Un banc de tenue à la décompression rapide en H2 pour la caractérisation des systèmes d’étanchéité et des matériaux élastomères et polymères ;
- Une presse de compression instrumentée dédiée à la caractérisation du comportement des étanchéités statiques pour assemblages à brides ;
- De cellules spécifiques de vieillissement de joints sous contraintes température pression, associées à des étuves haute température ATEX.
Les organes de régulation et de sécurité que sont les vannes industrielles ont aussi des moyens d’analyse dédiés pour caractériser à la fois leur endurance et le niveau d’émission fugitive qui leur est associé. Ces moyens mettront en œuvre :
- Des chambres à vide spécifiques ;
- Des étuves et enceintes climatiques.
Concevoir et fabriquer les structures composites de demain
Parmi les procédés de fabrication, HyMEET intègre une cellule robotisée de dernière génération, HySPIDE TP, dédiée à la fabrication de pièces thermoplastiques par dépose et consolidation in situ (en temps réel sans aucune autre étape nécessaire) par une chauffe laser. Elle permet notamment la production de réservoirs hydrogène de conception optimisée et durable pour le monde de la mobilité.
Nos experts sont également en mesure de contrôler les réservoirs par contrôles non destructifs.
D’autres équipements en cours d’acquisition viendront compléter ce parc machines pour notamment:
- Valider les équipements de contrôle et de mesure pour les circuits H2 ;
- Maîtriser les opérations de fabrication ;
- Evaluer la propreté des pièces ;
- Valider la résistance à la corrosion.